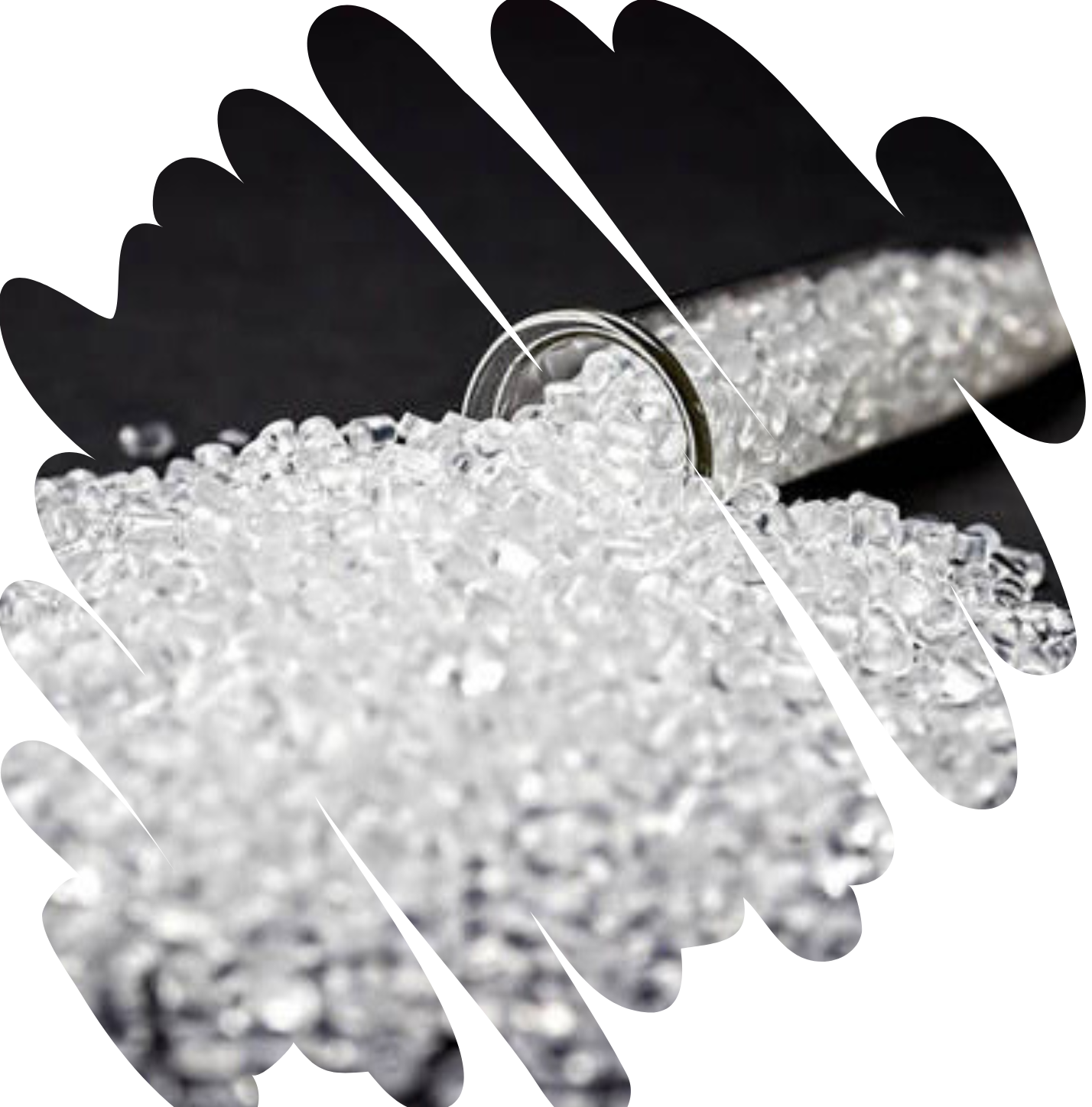
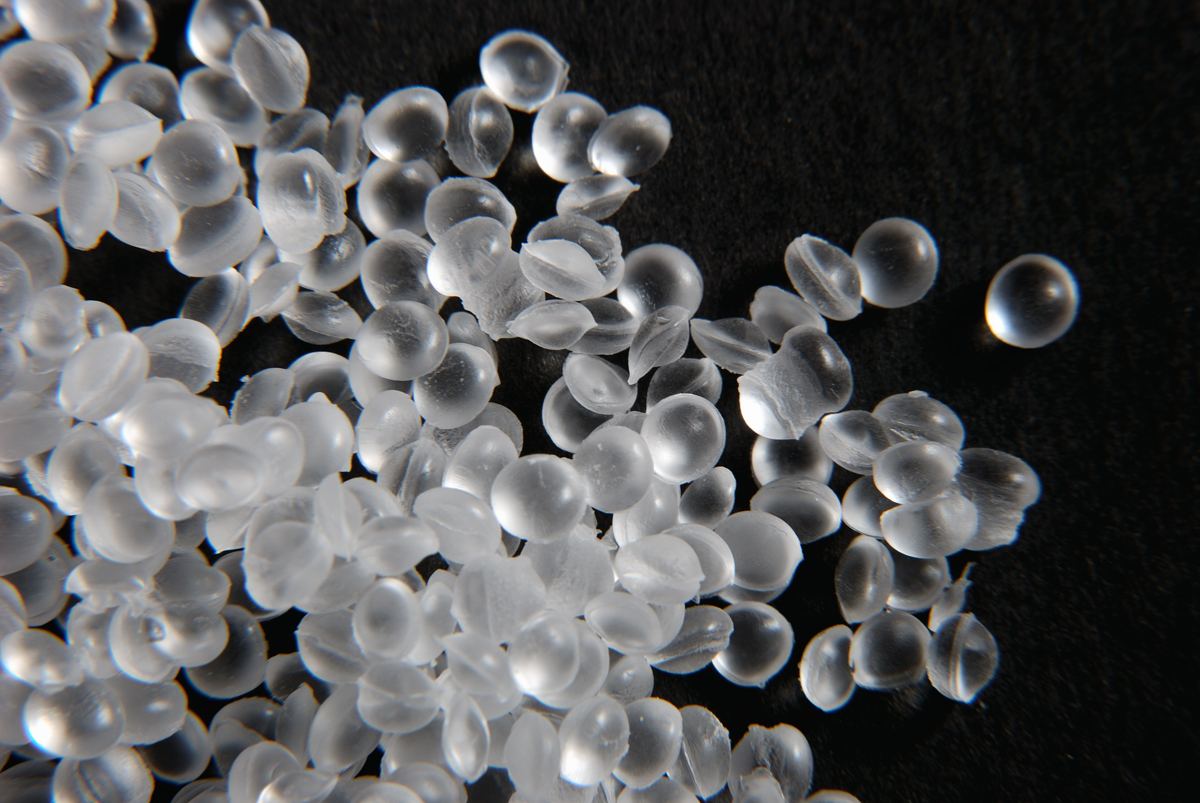
ਥਰਮੋਪਲਾਸਟਿਕ ਪੌਲੀਯੂਰੇਥੇਨ (ਟੀਪੀਯੂ) ਇੱਕ ਬਹੁਮੁਖੀ ਸਮੱਗਰੀ ਹੈ ਜੋ ਇਸਦੀ ਟਿਕਾਊਤਾ ਅਤੇ ਲਚਕੀਲੇਪਣ ਲਈ ਜਾਣੀ ਜਾਂਦੀ ਹੈ।ਹਾਲਾਂਕਿ, ਕੁਝ ਐਪਲੀਕੇਸ਼ਨਾਂ ਵਿੱਚ, ਟੀਪੀਯੂ ਗ੍ਰੈਨਿਊਲਜ਼ ਦੀ ਕਠੋਰਤਾ ਨੂੰ ਘਟਾਉਣ ਦੀ ਲੋੜ ਹੋ ਸਕਦੀ ਹੈ ਜਦੋਂ ਕਿ ਇੱਕੋ ਸਮੇਂ ਘਬਰਾਹਟ ਪ੍ਰਤੀਰੋਧ ਨੂੰ ਵਧਾਉਂਦੇ ਹੋਏ।
ਟੀ.ਪੀ.ਯੂ. ਦੀ ਕਠੋਰਤਾ ਨੂੰ ਘਟਾਉਣ ਅਤੇ ਘਬਰਾਹਟ ਪ੍ਰਤੀਰੋਧ ਸੰਤੁਲਨ ਨੂੰ ਬਿਹਤਰ ਬਣਾਉਣ ਲਈ ਰਣਨੀਤੀਆਂ।
1. ਨਰਮ ਸਮੱਗਰੀ ਨਾਲ ਮਿਲਾਉਣਾ
TPU ਦੀ ਕਠੋਰਤਾ ਨੂੰ ਘਟਾਉਣ ਦੇ ਸਭ ਤੋਂ ਸਿੱਧੇ ਤਰੀਕਿਆਂ ਵਿੱਚੋਂ ਇੱਕ ਹੈ ਇਸਨੂੰ ਇੱਕ ਨਰਮ ਥਰਮੋਪਲਾਸਟਿਕ ਸਮੱਗਰੀ ਨਾਲ ਮਿਲਾਉਣਾ।ਆਮ ਵਿਕਲਪਾਂ ਵਿੱਚ TPE (ਥਰਮੋਪਲਾਸਟਿਕ ਇਲਾਸਟੋਮਰ) ਅਤੇ TPU ਦੇ ਨਰਮ ਗ੍ਰੇਡ ਸ਼ਾਮਲ ਹੁੰਦੇ ਹਨ।
ਨਰਮ ਸਮੱਗਰੀ ਦੀ ਸਾਵਧਾਨੀ ਨਾਲ ਚੋਣ ਅਤੇ ਅਨੁਪਾਤ ਜਿਸ 'ਤੇ ਇਸਨੂੰ TPU ਨਾਲ ਮਿਲਾਇਆ ਜਾਂਦਾ ਹੈ, ਸਖਤਤਾ ਘਟਾਉਣ ਦੇ ਲੋੜੀਂਦੇ ਪੱਧਰ ਨੂੰ ਪ੍ਰਾਪਤ ਕਰਨ ਵਿੱਚ ਮਦਦ ਕਰ ਸਕਦਾ ਹੈ।
2. ਇੱਕ ਤਾਜ਼ਾ ਪਹੁੰਚ: ਨੋਵੇਲ ਸਾਫਟ ਮੈਟੀਰੀਅਲ Si-TPV ਨਾਲ TPU ਕਣਾਂ ਨੂੰ ਮਿਲਾਉਣਾ
SILIKE ਲਾਂਚ ਕੀਤੇ ਸਾਫਟ ਮਟੀਰੀਅਲ Si-TPV (ਡਾਇਨੈਮਿਕ ਵਲਕੈਨੀਜੇਟ ਥਰਮੋਪਲਾਸਟਿਕ ਸਿਲੀਕੋਨ-ਅਧਾਰਿਤ ਇਲਾਸਟੋਮਰ) ਦੇ ਨਾਲ 85A TPU ਗ੍ਰੈਨਿਊਲਸ ਨੂੰ ਮਿਲਾਉਣਾ, ਇਹ ਵਿਧੀ ਸਖਤਤਾ ਘਟਾਉਣ ਅਤੇ ਵਧੇ ਹੋਏ ਘਬਰਾਹਟ ਪ੍ਰਤੀਰੋਧ ਦੇ ਵਿਚਕਾਰ ਲੋੜੀਂਦੇ ਸੰਤੁਲਨ ਨੂੰ ਮਾਰਦੀ ਹੈ, ਇਸਦੇ ਹੋਰ ਲੋੜੀਂਦੇ ਗੁਣਾਂ ਨਾਲ ਸਮਝੌਤਾ ਕੀਤੇ ਬਿਨਾਂ।
TPU ਕਣਾਂ ਦੀ ਕਠੋਰਤਾ ਨੂੰ ਘਟਾਉਣ ਦਾ ਤਰੀਕਾ, ਫਾਰਮੂਲਾ ਅਤੇ ਮੁਲਾਂਕਣ:
85A TPU ਦੀ ਕਠੋਰਤਾ ਵਿੱਚ 20% Si-TPV ਜੋੜਨਾ ਕਠੋਰਤਾ ਨੂੰ 79.2A ਤੱਕ ਘਟਾ ਦਿੰਦਾ ਹੈ।
ਨੋਟ:ਉਪਰੋਕਤ ਟੈਸਟ ਡੇਟਾ ਸਾਡੀ ਲੈਬ ਪ੍ਰੈਕਟੀਕਲ ਟੈਸਟ ਡੇਟਾ ਹੈ, ਅਤੇ ਇਸ ਉਤਪਾਦ ਦੀ ਵਚਨਬੱਧਤਾ ਦੇ ਰੂਪ ਵਿੱਚ ਨਹੀਂ ਸਮਝਿਆ ਜਾ ਸਕਦਾ ਹੈ, ਗਾਹਕ ਨੂੰ ਉਹਨਾਂ ਦੇ ਆਪਣੇ ਖਾਸ ਦੇ ਅਧਾਰ ਤੇ ਟੈਸਟ ਕੀਤਾ ਜਾਣਾ ਚਾਹੀਦਾ ਹੈ.
ਹਾਲਾਂਕਿ, ਵੱਖੋ-ਵੱਖਰੇ ਮਿਸ਼ਰਣ ਅਨੁਪਾਤ ਦੇ ਨਾਲ ਪ੍ਰਯੋਗ ਆਮ ਹੈ, ਜਿਸਦਾ ਉਦੇਸ਼ ਕੋਮਲਤਾ ਅਤੇ ਘਬਰਾਹਟ ਪ੍ਰਤੀਰੋਧ ਦੇ ਅਨੁਕੂਲ ਸੁਮੇਲ ਨੂੰ ਪ੍ਰਾਪਤ ਕਰਨਾ ਹੈ।
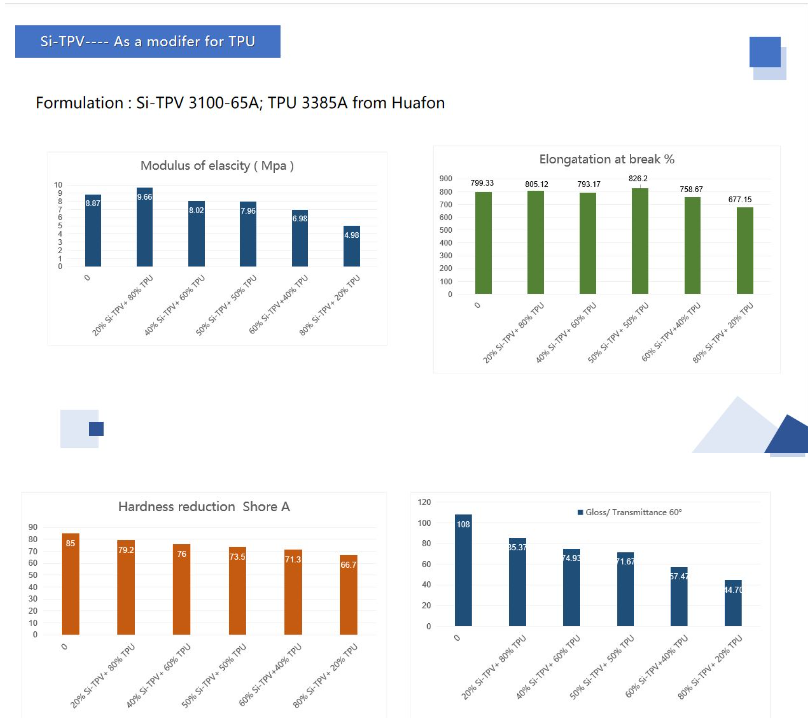
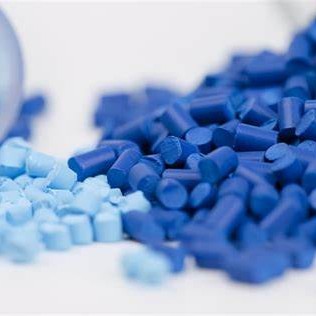
3. ਐਬਰੇਸ਼ਨ-ਰੋਧਕ ਫਿਲਰਾਂ ਨੂੰ ਸ਼ਾਮਲ ਕਰਨਾ
ਘਬਰਾਹਟ ਪ੍ਰਤੀਰੋਧ ਨੂੰ ਵਧਾਉਣ ਲਈ, ਮਾਹਰ ਖਾਸ ਫਿਲਰ ਜਿਵੇਂ ਕਿ ਕਾਰਬਨ ਬਲੈਕ, ਗਲਾਸ ਫਾਈਬਰਸ, ਸਿਲੀਕੋਨ ਮਾਸਟਰਬੈਚ, ਜਾਂ ਸਿਲੀਕਾਨ ਡਾਈਆਕਸਾਈਡ ਨੂੰ ਸ਼ਾਮਲ ਕਰਨ ਦਾ ਸੁਝਾਅ ਦਿੰਦੇ ਹਨ।ਇਹ ਫਿਲਰ TPU ਦੇ ਪਹਿਨਣ-ਰੋਧਕ ਗੁਣਾਂ ਨੂੰ ਮਜ਼ਬੂਤ ਕਰ ਸਕਦੇ ਹਨ।
ਹਾਲਾਂਕਿ, ਇਹਨਾਂ ਫਿਲਰਾਂ ਦੀ ਮਾਤਰਾ ਅਤੇ ਫੈਲਾਅ 'ਤੇ ਧਿਆਨ ਨਾਲ ਵਿਚਾਰ ਕੀਤਾ ਜਾਣਾ ਚਾਹੀਦਾ ਹੈ, ਕਿਉਂਕਿ ਬਹੁਤ ਜ਼ਿਆਦਾ ਮਾਤਰਾ ਸਮੱਗਰੀ ਦੀ ਲਚਕਤਾ ਨੂੰ ਪ੍ਰਭਾਵਤ ਕਰ ਸਕਦੀ ਹੈ।
4. ਪਲਾਸਟਿਕਾਈਜ਼ਰ ਅਤੇ ਨਰਮ ਕਰਨ ਵਾਲੇ ਏਜੰਟ
TPU ਕਠੋਰਤਾ ਨੂੰ ਘਟਾਉਣ ਲਈ ਇੱਕ ਢੰਗ ਵਜੋਂ, TPU ਨਿਰਮਾਤਾ ਪਲਾਸਟਿਕਾਈਜ਼ਰ ਜਾਂ ਨਰਮ ਕਰਨ ਵਾਲੇ ਏਜੰਟਾਂ ਦੀ ਵਰਤੋਂ ਕਰ ਸਕਦੇ ਹਨ।ਇੱਕ ਢੁਕਵੇਂ ਪਲਾਸਟਿਕਾਈਜ਼ਰ ਦੀ ਚੋਣ ਕਰਨਾ ਮਹੱਤਵਪੂਰਨ ਹੈ ਜੋ ਘਬਰਾਹਟ ਪ੍ਰਤੀਰੋਧ ਨਾਲ ਸਮਝੌਤਾ ਕੀਤੇ ਬਿਨਾਂ ਕਠੋਰਤਾ ਨੂੰ ਘਟਾ ਸਕਦਾ ਹੈ।TPU ਨਾਲ ਵਰਤੇ ਜਾਣ ਵਾਲੇ ਆਮ ਪਲਾਸਟਿਕਾਈਜ਼ਰਾਂ ਵਿੱਚ ਡਾਇਓਕਟਾਈਲ ਫਥਾਲੇਟ (ਡੀਓਪੀ) ਅਤੇ ਡਾਇਓਕਟਾਈਲ ਐਡੀਪੇਟ (ਡੀਓਏ) ਸ਼ਾਮਲ ਹਨ।ਇਹ ਯਕੀਨੀ ਬਣਾਉਣ ਲਈ ਧਿਆਨ ਰੱਖਿਆ ਜਾਣਾ ਚਾਹੀਦਾ ਹੈ ਕਿ ਚੁਣਿਆ ਗਿਆ ਪਲਾਸਟਿਕਾਈਜ਼ਰ TPU ਦੇ ਅਨੁਕੂਲ ਹੈ ਅਤੇ ਹੋਰ ਵਿਸ਼ੇਸ਼ਤਾਵਾਂ ਜਿਵੇਂ ਕਿ ਤਣਾਅ ਦੀ ਤਾਕਤ ਜਾਂ ਰਸਾਇਣਕ ਪ੍ਰਤੀਰੋਧ ਨੂੰ ਨਕਾਰਾਤਮਕ ਤੌਰ 'ਤੇ ਪ੍ਰਭਾਵਿਤ ਨਹੀਂ ਕਰਦਾ ਹੈ।ਇਸ ਤੋਂ ਇਲਾਵਾ, ਲੋੜੀਂਦੇ ਸੰਤੁਲਨ ਨੂੰ ਬਣਾਈ ਰੱਖਣ ਲਈ ਪਲਾਸਟਿਕਾਈਜ਼ਰਾਂ ਦੀ ਖੁਰਾਕ ਨੂੰ ਸਾਵਧਾਨੀ ਨਾਲ ਨਿਯੰਤਰਿਤ ਕੀਤਾ ਜਾਣਾ ਚਾਹੀਦਾ ਹੈ।
5. ਫਾਈਨ-ਟਿਊਨਿੰਗ ਐਕਸਟਰਿਊਸ਼ਨ ਅਤੇ ਪ੍ਰੋਸੈਸਿੰਗ ਪੈਰਾਮੀਟਰ
ਘਟੀ ਹੋਈ ਕਠੋਰਤਾ ਅਤੇ ਵਧੇ ਹੋਏ ਘਬਰਾਹਟ ਪ੍ਰਤੀਰੋਧ ਦੇ ਲੋੜੀਂਦੇ ਸੁਮੇਲ ਨੂੰ ਪ੍ਰਾਪਤ ਕਰਨ ਲਈ ਐਕਸਟਰਿਊਸ਼ਨ ਅਤੇ ਪ੍ਰੋਸੈਸਿੰਗ ਮਾਪਦੰਡਾਂ ਨੂੰ ਅਡਜਸਟ ਕਰਨਾ ਮਹੱਤਵਪੂਰਨ ਹੈ।ਇਸ ਵਿੱਚ ਐਕਸਟਰਿਊਸ਼ਨ ਦੌਰਾਨ ਤਾਪਮਾਨ, ਦਬਾਅ, ਅਤੇ ਕੂਲਿੰਗ ਦਰਾਂ ਵਰਗੇ ਮਾਪਦੰਡਾਂ ਨੂੰ ਸੋਧਣਾ ਸ਼ਾਮਲ ਹੈ।
ਘੱਟ ਐਕਸਟਰਿਊਸ਼ਨ ਤਾਪਮਾਨ ਅਤੇ ਸਾਵਧਾਨੀਪੂਰਵਕ ਕੂਲਿੰਗ ਘਬਰਾਹਟ-ਰੋਧਕ ਫਿਲਰਾਂ ਦੇ ਫੈਲਾਅ ਨੂੰ ਅਨੁਕੂਲ ਬਣਾਉਂਦੇ ਹੋਏ ਨਰਮ TPU ਦੀ ਅਗਵਾਈ ਕਰ ਸਕਦੀ ਹੈ।
6. ਪੋਸਟ-ਪ੍ਰੋਸੈਸਿੰਗ ਤਕਨੀਕਾਂ
ਪੋਸਟ-ਪ੍ਰੋਸੈਸਿੰਗ ਤਕਨੀਕਾਂ ਜਿਵੇਂ ਕਿ ਐਨੀਲਿੰਗ, ਸਟ੍ਰੈਚਿੰਗ, ਜਾਂ ਸਤਹ ਦੇ ਇਲਾਜ ਵੀ ਕਠੋਰਤਾ ਨਾਲ ਸਮਝੌਤਾ ਕੀਤੇ ਬਿਨਾਂ ਘਬਰਾਹਟ ਪ੍ਰਤੀਰੋਧ ਨੂੰ ਹੋਰ ਵਧਾ ਸਕਦੇ ਹਨ।
ਐਨੀਲਿੰਗ, ਖਾਸ ਤੌਰ 'ਤੇ, TPU ਦੀ ਕ੍ਰਿਸਟਲਿਨ ਬਣਤਰ ਨੂੰ ਸੁਧਾਰ ਸਕਦਾ ਹੈ, ਇਸ ਨੂੰ ਪਹਿਨਣ ਅਤੇ ਅੱਥਰੂ ਕਰਨ ਲਈ ਵਧੇਰੇ ਰੋਧਕ ਬਣਾਉਂਦਾ ਹੈ।
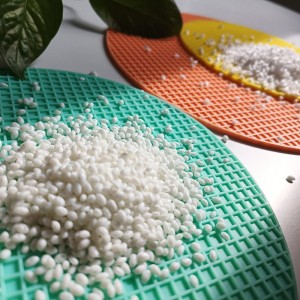
ਸਿੱਟੇ ਵਜੋਂ, ਘਟੀ ਹੋਈ TPU ਕਠੋਰਤਾ ਅਤੇ ਸੁਧਰੇ ਹੋਏ ਘਬਰਾਹਟ ਪ੍ਰਤੀਰੋਧ ਦੇ ਨਾਜ਼ੁਕ ਸੰਤੁਲਨ ਨੂੰ ਪ੍ਰਾਪਤ ਕਰਨਾ ਇੱਕ ਬਹੁਪੱਖੀ ਪ੍ਰਕਿਰਿਆ ਹੈ।TPU ਨਿਰਮਾਤਾ ਸਮੱਗਰੀ ਦੀ ਚੋਣ, ਮਿਸ਼ਰਣ, ਘਿਰਣਾ-ਰੋਧਕ ਫਿਲਰ, ਪਲਾਸਟਿਕਾਈਜ਼ਰ, ਨਰਮ ਕਰਨ ਵਾਲੇ ਏਜੰਟ, ਅਤੇ ਕਿਸੇ ਦਿੱਤੇ ਐਪਲੀਕੇਸ਼ਨ ਦੀਆਂ ਵਿਲੱਖਣ ਜ਼ਰੂਰਤਾਂ ਦੇ ਨਾਲ ਇਕਸਾਰ ਹੋਣ ਲਈ ਪਦਾਰਥਕ ਵਿਸ਼ੇਸ਼ਤਾਵਾਂ ਨੂੰ ਵਧੀਆ-ਟਿਊਨ ਕਰਨ ਲਈ ਐਕਸਟਰਿਊਸ਼ਨ ਪੈਰਾਮੀਟਰਾਂ ਦੇ ਸਹੀ ਨਿਯੰਤਰਣ ਦਾ ਲਾਭ ਲੈ ਸਕਦੇ ਹਨ।
ਇਹ ਉਹ ਹੈ ਜੋ ਤੁਹਾਨੂੰ ਇੱਕ ਜਿੱਤਣ ਵਾਲੇ ਫਾਰਮੂਲੇ ਦੀ ਲੋੜ ਹੈ ਜੋ TPU ਕਣਾਂ ਦੀ ਕਠੋਰਤਾ ਨੂੰ ਘਟਾਉਂਦਾ ਹੈ ਅਤੇ ਘਬਰਾਹਟ ਪ੍ਰਤੀਰੋਧ ਨੂੰ ਸੁਧਾਰਦਾ ਹੈ!
ਸਿਲੀਕੇ ਨਾਲ ਸੰਪਰਕ ਕਰੋ, ਸਾਡਾ Si-TPV ਤੁਹਾਡੇ TPU ਕਣ-ਆਧਾਰਿਤ ਉਤਪਾਦਾਂ ਲਈ ਆਦਰਸ਼ ਨਰਮਤਾ, ਲਚਕਤਾ, ਟਿਕਾਊਤਾ, ਸਤਹ ਮੈਟ ਪ੍ਰਭਾਵ, ਅਤੇ ਹੋਰ ਜ਼ਰੂਰੀ ਵਿਸ਼ੇਸ਼ਤਾਵਾਂ ਨੂੰ ਪ੍ਰਾਪਤ ਕਰਨ ਵਿੱਚ ਤੁਹਾਡੀ ਮਦਦ ਕਰਦਾ ਹੈ!
ਸੰਬੰਧਿਤ ਖ਼ਬਰਾਂ

